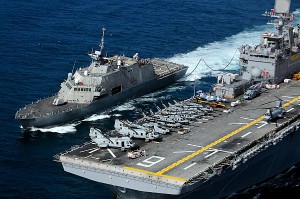
Sooo…who remembers, waaay back in February 2009, when a desperate NAVSEA was looking to get 3-5 tons off the LCS-1? Remember what they wanted to take out? I do. From Janes:
Naval Sea Systems Command (NAVSEA) told Jane’s that officials are considering taking out components “that have become unused on the finished ship”. The proposed list includes engine removal rails for the twin Rolls-Royce MT-30 gas turbines.
It seems the ghost of contingencies past paid LCS-1 a little visit earlier this month. According to some breaking news out of Navy Times, MT-30 turbines, ah, break a bit faster than originally expected (wonder how thorough the regular maintenance has
been, eh? Maybe a manning issue coming home to roost?).
I guess it is time to ask if those fancy LCS-1 bustles obviated the removal of the engine removal rails or not…because it certainly sounds like the turbine replacement hasn’t been done yet and that, two weeks after the turbine died, LCS-1 is still sidelined.
I do hope the bright person at NAVSEA who proposed landing the removal rails has been thoroughly and vigorously mocked. And then re-assigned to Greenland or something.
{ 6 comments… read them below or add one }
NAVSEA never learns from their mistakes. They are in a major weight reducion mode for the JHSV and cutting any extra weight not directly tied to mission.
I serve on a gas turbine ship, and ship’s maintenance can have a pretty significant effect on the performance of a GTE, particularly if the regular water washes aren’t conducted, the resulting flow can cause (usually) stalls and failure to fire, and if they’re bad enough, the engine will eat itself up just like LCS-1 appears to have done.
In defense of LCS, though, I’ve also seen brand new out of the box engines eat themselves up (blades balanced incorrectly, FOD, etc.), so it can be kind of random, too. But when I read the story, the water washes were the first thing that came to mind.
Just a WAG, but maintaining fuel integrity might be a problem. Don’t know how automated that is, but sometimes tired humans can do stupid things. But, then again, cracks in the fuel tanks probably didn’t help matters, either.
Guys from Lockheed don’t make mean comments about broken stuff that they just bought and installed. 😛
Blade failure, it seems to me, could be caused by (1) air and tiny particulates flowing over the blades [erosion]; (2) ingestion of large objects [foreign object damage]; and (3) thermal cycling leading to propagation of a flaw through the material [manufacturing defect].
Only one of those potential failure modes can be related to anything the crew might have done – FOD. Given that they were underway at the time of the failure, odds are very slim that anyone had been inside the engine module. If anything, the small crew would decrease the likelihood of a GSM doing preventive maintenance that would require module entry.
I’d be interested in your thoughts on what failure modes might be caused by (or related to) reduced manning.
But if I blamed it on a manufacturing defect those guys from Lockheed will come here and make mean comments!!! (just kidding)
Yeah, we’ll have to wait for the failure analysis, but I can see some scenarios where manning might contribute to operational conditions that accelerate blade wear and/or increase risk of blade failure..
Bit of a stretch to relate manning and turbine blade fatigue life, dontcha think?